When you're faced with a large hole in your roof, it can seem like a daunting challenge. Yet, with the right guidance and materials, you can tackle this problem head-on. This can save time and money you'd otherwise spend on a professional roofer like CJ Commercial Roofing NJ.
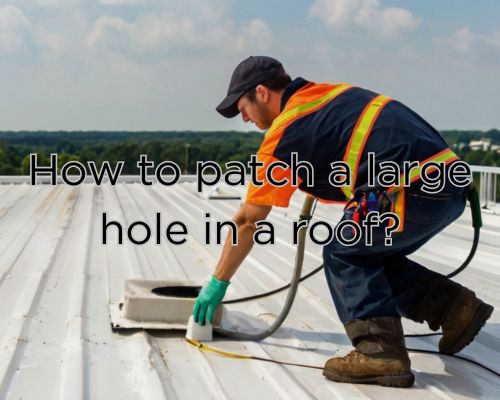
To patch a large hole in your roof, you'll need to prepare the area, secure the patch, and ensure it's waterproof.
You'll begin by clearing the area around the damaged section and organizing your tools. This preparation sets the stage for an effective repair.
Next, carefully install new roofing materials over the hole. Make sure to extend them past the damaged area to ensure a secure fix.
Finishing touches like applying roofing tar and fitting shingles ensure the patch blends seamlessly with your existing roof. This methodical approach turns a complex task into a manageable DIY roof repair.
Preparing for the Repair
Proper preparation ensures a safe and effective repair. You'll need to focus on safety measures, thoroughly assess the damage, and gather the right tools and materials.
Safety First
Prioritize safety before starting any repair. Wear appropriate safety gear such as gloves, rubber-soled shoes, and a helmet to prevent injuries.
Use an extension ladder that is securely positioned and stabilized against the house. Ropes and hooks can be used to attach the ladder to the fascia, providing additional stability.
Avoid overloading your hands when climbing the ladder. Instead, use a tool belt.
Make sure the working area is free from debris to prevent accidents. Consider enlisting a helper to assist with handing tools and materials up to the roof.
Assessing the Damage
Conduct a thorough roof inspection to understand the extent of the damage. Identify all problem areas, focusing on visible cracks, holes, and signs of water damage.
Look for signs of moisture beneath shingles, inside the attic, or on the ceiling. Checking for leaks early can help prevent further damage to the structure.
Use a flashlight to look for any dark spots, mold, or rot that might indicate water seepage.
Document the damaged areas with photos for reference. This will help you determine the amount and type of materials you'll need for the repair.
Gathering Necessary Tools and Materials
Collect all the necessary tools and materials before starting the repair.
Essential tools include a hammer, pry bar, utility knife, and roofing nails.
You'll also need roofing materials such as shingles, plywood, tar paper, roofing tar, and roofing cement.
For sealing and patching, prepare appropriate patching material that fits the type of roof you have.
Make sure you have enough roofing nails and cement to secure everything in place.
Organize your tools and materials in a way that allows easy access and mobility once you're on the roof. This preparation will make the repair process smoother and more efficient.
Executing the Repair
Repairing a large hole in your roof involves removing damaged materials, installing the patch, and finishing to ensure waterproofing. Proper attention at each step will help prevent future water penetration and structural issues. But if you find it hard to do, just refer it to CJ Commercial Roofing NJ.
Removing Damaged Materials
First, assess the damaged area to determine the extent of the work needed.
Use a pry bar to remove the damaged shingles and roofing nails around the hole. Be careful when prying to avoid causing additional damage to the surrounding roof decking.
Next, cut away any damaged roof decking using a reciprocating saw. Ensure you cut back to the nearest rafters for proper support when installing the patch.
Clear the area of any debris to prepare for the next steps.
Installing the Patch
Measure the hole and cut a piece of plywood or roof decking to fit, with at least a six-inch overlap on all sides.
Place the new decking over the hole and secure it to the roof rafters using nails or screws.
Cover the new decking with roofing felt or tar paper, ensuring it overlaps the existing materials by at least 2 inches. Secure it with roofing nails.
For roof shingles, cut new shingles to size and slide them under the row above, aligning with adjacent shingles. Nail them into place, ensuring the nails are covered by the above row.
Finishing and Waterproofing
To seal the patch, apply roofing tar or liquid nails around the edges of the new decking and shingles. Spread it evenly to cover small cracks and ensure a waterproof seal.
If using metal flashing, place it over the patch and secure it with roofing nails. Then, cover the seams with roofing cement.
Finally, inspect the entire patched area for gaps or exposed nails. Apply caulk to any small gaps or cracks to ensure complete waterproofing.
Monitor the patch over the next few days, especially after any rain, to confirm it remains watertight.