Guttering plays a vital role in protecting your property from water damage by directing rainwater away from the foundation, walls, and roof. In Melbourne, with its unique weather patterns, ensuring that your guttering is properly clipped and maintained is critical to prevent structural damage. This article delves into the importance of gutter clips, the recommended frequency for clipping, and why this matters specifically for Melbourne homeowners.
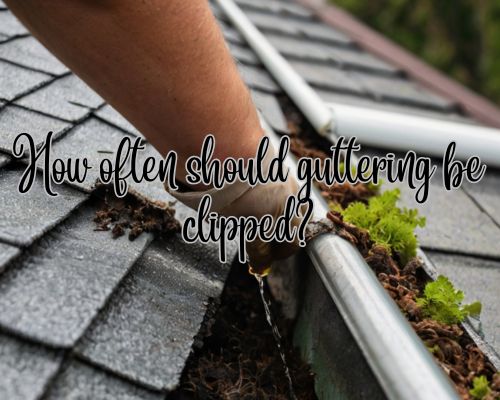
Why Gutter Clipping Matters
Gutter clips secure the guttering system to your property, ensuring it remains in place during heavy rain or high winds. Proper clipping prevents sagging, leaks, and eventual gutter collapse. For Melbourne homeowners, this is especially important given the city's unpredictable weather, which includes sudden downpours and gusty winds that can strain inadequately secured gutters.
Additionally, poorly clipped gutters can lead to water overflow, damaging walls, fascia boards, and landscaping. For heritage homes in Melbourne, which are often characterized by intricate architecture, improperly maintained guttering can result in costly repairs and detract from the property's aesthetic value.
How Often Should Guttering Be Clipped?
The frequency of gutter clipping depends on various factors such as the type of guttering, the materials used, and the specific weather conditions in your area. For Melbourne homeowners, it is recommended to check and secure gutter clips:
- Every Two to Three Years: For standard homes, an inspection every two to three years is generally sufficient. During these inspections, replace any broken or loose clips to ensure the guttering remains secure.
- After Severe Weather Events: Melbourne’s weather can be unpredictable, with sudden storms and high winds. After such events, inspect your guttering system to ensure no clips have loosened or been damaged.
- When Installing New Guttering: If you're replacing or installing new gutters, ensure the gutter clips are spaced correctly. Most experts recommend a spacing of 900mm (35 inches) for standard gutters or 600mm (24 inches) for areas prone to heavy rain, such as Melbourne.
For professional work, see https://gutter-cleaning-melbourne.com.au/.
Factors Affecting Gutter Clipping in Melbourne
Several factors unique to Melbourne can impact how often your guttering should be clipped:
- Tree Coverage: Melbourne's leafy suburbs like Kew, Hawthorn, and Camberwell are beautiful but can pose challenges for gutter maintenance. Fallen leaves and debris can strain guttering systems, making secure clips even more essential.
- Rainfall Patterns: Melbourne experiences an average annual rainfall of 650mm, with peaks during winter and spring. Prolonged exposure to rain can weaken gutter clips, especially if the system isn’t regularly maintained.
- Temperature Fluctuations: Melbourne’s climate can swing from hot summers to cool winters, which can cause expansion and contraction of gutter materials, potentially loosening clips over time.
Types of Gutter Clips and Their Importance
Choosing the right type of gutter clip can make a significant difference in maintaining the longevity of your guttering system. Common types include:
- Snap Clips: Ideal for standard aluminum gutters, these clips are cost-effective and easy to install.
- Hidden Hangers: These provide a sleek look by being concealed within the gutter system. They’re great for modern Melbourne homes seeking a minimalist aesthetic.
- Fascia Brackets: These heavy-duty clips are designed for areas prone to high winds and are perfect for Melbourne’s storm-prone seasons.
Professional Gutter Maintenance in Melbourne
While DIY inspections are helpful, hiring a professional gutter maintenance service ensures a thorough job. Professionals can:
- Assess the condition of your guttering system.
- Replace or reinforce gutter clips as needed.
- Provide tailored advice for your Melbourne property, considering local weather conditions and architectural factors.
Companies specializing in gutter maintenance in Melbourne often offer additional services such as gutter cleaning and repair. Regular professional maintenance not only prolongs the life of your guttering but also saves you from costly repairs in the future, see https://gutter-cleaning-melbourne.com.au/.
Local Regulations and Considerations
In Melbourne, local building codes may dictate the type of guttering and clipping required, especially for new constructions or significant renovations. For example, bushfire-prone areas like the Dandenong Ranges require compliance with strict guttering standards to minimize fire risk. Ensure your guttering system meets these regulations and is appropriately clipped to adhere to safety requirements.
DIY Tips for Gutter Clipping
If you decide to inspect or secure your gutter clips yourself, here are a few tips:
- Safety First: Always use a stable ladder and have someone nearby to assist you.
- Check Spacing: Ensure clips are evenly spaced according to the type of guttering and local rainfall requirements.
- Use Quality Materials: Invest in high-quality clips suited to Melbourne's climate to prevent frequent replacements.
- Inspect Regularly: Create a maintenance schedule that aligns with Melbourne’s seasonal changes.
Conclusion
Maintaining your guttering system by ensuring it is properly clipped is crucial for Melbourne homeowners. Given the city’s variable weather, investing in regular inspections and maintenance can save you significant time and money in the long run. Whether you’re a homeowner in Brighton, Richmond, or Essendon, taking a proactive approach to gutter clipping ensures your property remains protected from water damage year-round.
For Melbourne-specific advice or professional assistance, consider reaching out to local gutter maintenance experts. Proper care today will ensure your guttering system serves you efficiently for years to come.